How CNC Machining Facilitates the Use of Recycled Copper in Manufacturing
Copper CNC machining is a progressively preferred approach in producing that leverages the accurate, automated capacities of Computer Numerical Control (CNC) innovation to create intricate elements from copper. Copper's distinct residential or commercial properties, including superb conductivity, corrosion resistance, and machinability, make it a very in-demand material in a variety of markets such as electronics, automotive, aerospace, and telecoms. The combination of copper's helpful qualities and progressed machining techniques makes it possible for makers to produce parts with high precision and lowered lead time, dramatically pushing the borders of development. CNC machining enables intricate geometries that would be impossible or hard to accomplish with traditional machining strategies, making it suitable for the production of detailed components, such as ports, warmth sinks, and housings.The process of CNC machining involves the usage of a computer to control device tools for a much more trusted and consistent result. Specialized strategies and devices are often used to maximize the machining process, which can include utilizing reducing devices covered with hard materials to lessen wear and boost efficiency when working with soft metals like copper.
Discover copper cnc machining exactly how copper CNC machining combines sophisticated technology with sustainable techniques to generate complex, high-precision parts, driving technology throughout sectors such as electronic devices, vehicle, and aerospace.
Amongst the main advantages of CNC machining copper is the ability to create complicated shapes that traditional machining methods may not accommodate. The high accuracy possible via CNC modern technology enables makers to produce firmly toleranced features that are crucial in numerous applications. In the electronics market, for instance, the demand for components with marginal resistances is vital, as electronic gadgets lessen and more intricate. CNC machining promotes the manufacturing of micro-components with such great tolerances, enabling innovations in clever gadgets, wearable technology, and other customer electronic devices. The repeatability of the CNC machining process ensures that mass production of copper parts keeps harmony, therefore satisfying strict market standards.
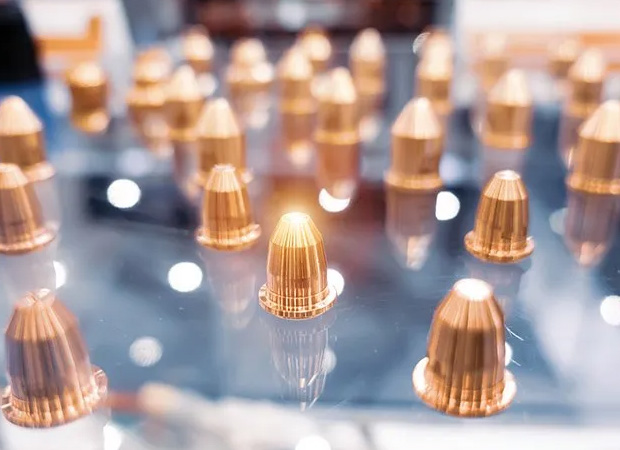
Temperature monitoring plays an important role in the CNC machining of copper due to its capability to conduct warm rapidly. High-speed machining can lead to considerable heat generation, which might adversely impact the residential or commercial properties of the copper and aggravate tool wear.
The sustainability facet of CNC machining copper is not to be overlooked. CNC machining, coupled with sustainable techniques, can lower waste by allowing producers to use scrap copper from various other procedures.
Along with sustainability, cost-effectiveness is one more essential variable for manufacturers selecting CNC machining for copper elements. Though the first investment in CNC machinery might be significant, the long-term benefits can exceed the prices. CNC machining provides a reduction in labor expenses as a result of its automated nature and reduces the demand for considerable manual intervention. Additionally, the exact control & repeatability supplied by CNC technology decreases scrap prices, lowering material costs. In addition, for small to medium batch production runs, CNC machining can show a lot more cost-effective contrasted to standard machining procedures, as it enables smooth adjustments and design changes without comprehensive retooling. This capability to pivot rapidly can be helpful, specifically in hectic markets where market needs can move suddenly.
In addition, as modern technology advances, the performances within CNC systems are increasing, further boosting the capacities of copper machining. The assimilation of simulation software application enables producers to forecast possible concerns prior to the machining process begins. These simulations make it possible for far better preparation of tool paths and clarify just how the copper product will respond throughout the machining procedure. By recognizing and resolving possible difficulties beforehand, business can minimize downtime and increase performance, developing a smoother functional flow.
Knowledgeable machinists should be adept in translating layout specs, selecting the proper devices, and changing machining criteria to reduce concerns connected with copper's unique machining attributes. Hybrid machining, which integrates traditional CNC machining techniques with additive production, is emerging as a feasible method for creating intricate copper elements, mixing the strengths of both modern technologies and potentially changing exactly how manufacturers come close to copper manufacturing.
In the realm of research study and development, CNC machining is helping the expedition of new copper alloys to boost performance additionally. By manufacturing copper with materials such as light weight aluminum, nickel, or tin, producers can craft compounds that have boosted strength, electrical efficiency, and resistance to wear and rust. These innovations might bring about emerging applications in markets that count heavily on conductive materials, such as sustainable power and electric automobiles. As global markets work towards greater energy effectiveness, copper's duty as a conductor in electronic circuits will stay extremely important, driving need for advanced machining services.
The aerospace and automotive industries are also keen adopters of copper CNC machining, especially where light-weight parts are of critical significance. The combination of copper's light-weight nature and superb electric and thermal conductivity makes it an ideal choice for elements such as electric calls, heat exchangers, and electrical wiring systems. As the change towards electrical and hybrid cars proceeds, the need for high-performance copper parts will likely surge, thereby driving the demand for innovative CNC machining techniques that make certain performance and top quality in manufacturing. From a manufacturing standpoint, the ability to innovate rapidly and deliver precision-engineered parts becomes progressively important in dealing with the emerging demands of these fast-evolving markets.
As CNC machining technology remains to develop, it permits further automation, where basic procedures such as device modifications, assessments, and maintenance can be configured into the production cycle. This evolution suggests that suppliers will certainly have the ability to attain greater efficiency degrees, much shorter lead times, and greater flexibility in accommodating custom demands or variants in layout. As an outcome, services that involve in CNC machining operations are better suited to pivot in response to the shifts in consumer and market needs, cultivating development in a progressively competitive landscape.
Discover countersink size chart how copper CNC machining merges innovative modern technology with sustainable techniques to generate complex, high-precision elements, driving development across sectors such as electronics, auto, and aerospace.
The worldwide marketplace for CNC machining of copper is observing considerable development, influenced by variables such as the increase of smart modern technologies, electric lorries, and ongoing initiatives to improve power effectiveness across numerous applications. In this evolution, ability and training growth stay extremely important; investing in labor force education on CNC machining methods, innovations, and product sciences will certainly empower makers to remain ahead of the contour.
To conclude, the assimilation of CNC machining with copper materials supplies a distinctive affordable edge for makers in today's busy industrial landscape. Its capacity to deliver high accuracy, reduce manufacturing time, and enable complicated designs makes CNC machining a crucial component of contemporary production practices. Paired with sustainability efforts, cost-effectiveness, and possibilities for development, the CNC machining of copper not just meets the demands of modern applications but likewise lays the foundation for the future trajectory of manufacturing in several fields. As markets progress and the boundaries of innovation increase, embracing CNC machining's capacity will certainly be essential to recognizing extraordinary growth and development in the use of copper items. The synergy of copper's material properties with sophisticated CNC machining methods proclaims a new age in which accuracy, performance, and sustainability work hand-in-hand to produce advanced parts that will certainly define the future of production and beyond.